Behind the Seams: Zane Yielding, Getting Wrangler® From our Distribution Center to Your Doorstep
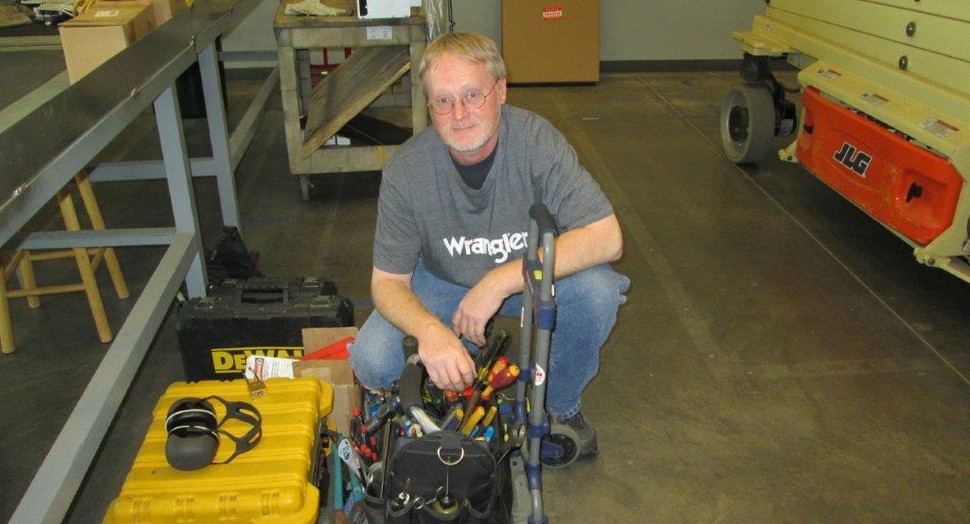
In Hackleburg, Alabama, the fast-paced energy at Kontoor’s distribution center can be felt from the floor to the forklift. And at the center of it is Zane Yielding, who recently became Facility Maintenance Technician, where he helps ensure seamless operations for fulfilling customer orders. Kontoor’s distribution centers are a critical part of the customer experience. From the moment a customer puts in an order, it’s sent to pickers who secure the merchandise for fulfillment, supported by team members ensuring everything is tracked and organized.
A dedicated 25-year employee, Zane’s vast knowledge of the distribution center’s processes, systems and networks has made him an invaluable asset. Combined with his positive outlook and values rooted in teamwork, Zane helps create a winning work environment.
“Where you work is kind of like your second home, so it’s a very family-oriented environment. I always look forward to seeing everyone,” said Zane. “We help each other succeed.”
We caught up with Zane in the middle of the busy holiday fulfillment season to learn more about his approach to developing a successful career.
Can you tell us about your career journey?
I was recently promoted to Facility Maintenance Technician, but I started in the shipping department in 1994. Then I moved into order picking, then stocking, and eventually got the title of Lead High Bay Operator, where all of our inventory is housed. I've been in just about every department here through the years.
What do you find interesting about your work?
I was actually on the testing team when they were constructing our current building and setting up all the conveyers, systems, and how things would be laid out, installed and tested. That was very interesting to me – to be able to assist in getting all the wrinkles out and help create an efficient setup.
What kind of changes have you seen in 25 years on the job?
Technology, for one. When we first started, it was basically just handheld scanners. And most things, even inventory, were done on sheets of paper. You’d use that to find the product location, find the box, take it over to a person, put the order together, pack it and put the stickers on. Eventually when e-commerce started blowing up, everything became much more automated. Now, it’s just amazing how much depth there is to our systems. I find the work fascinating and have tried to learn every bit of the ins and outs, because knowledge is power.
What is something surprising about your line of work?
When you do this job, you are always trying to make sure things run smoothly. If you can anticipate a problem and catch it ahead of time, then no one will realize there might have been a problem to begin with. You’re looking for things to fix before they even break, so that the process always run smoothly. If everyone is doing their job, we’re that invisible layer between the customer ordering and receiving our product. We take pride in our work, and in our teamwork.
What’s in Zane’s closet
Wrangler Men’s Five Star Premium Carpenter Jean. “They’re straight-up comfort. There’s something to be said for a functional pair of jeans. I’m definitely a Wrangler customer as well as an employee, and I wear them everywhere.”