Behind the Seams: Margarita Pasakarnis Takes us Inside the Virtual World of Fashion Design
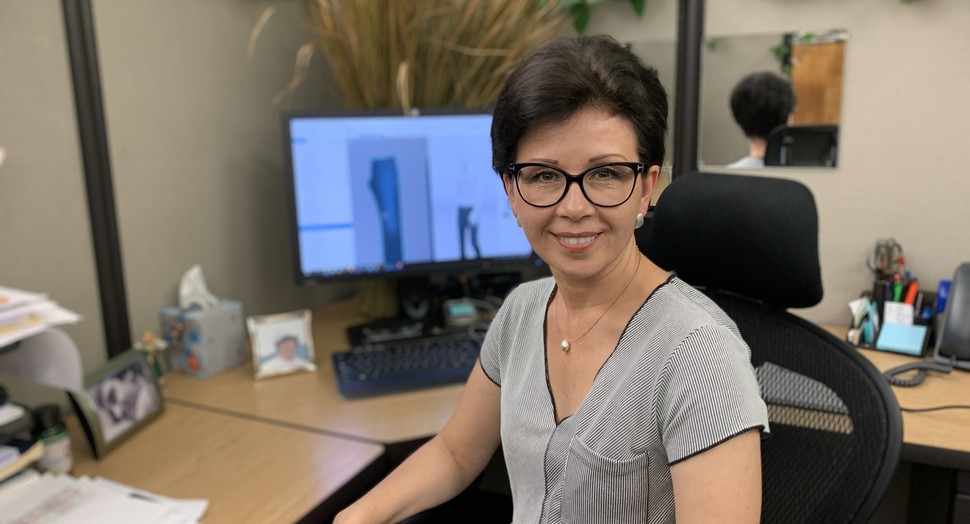
Margarita Pasakarnis leads Kontoor Brands’ 3D Design Center of Excellence with a passion for everything she creates. With more than 30 years in the industry, technology is starting to catch up with the visions she’s dreamt of for decades. Today, she’s pushing Kontoor forward using the industry’s most innovative methods. Pasakarnis weaves her extensive experience in design, product development and manufacturing - helping implement 3D technologies into the end-to-end workflow, from concept to manufacturing.
“Fashion is a language,” Pasakarnis said. “I look at the way people dress as the way they talk.”
Communication has been a major theme in Pasakarnis’ career—and provides an insight into her adaptability. When she first came to the United States, she didn’t speak a word of English. After completing her apparel construction engineering degree in Belarus, she moved to Rhode Island, quickly realizing New York was the place to be for fashion. “It was like dropping a cat in water,” she said. “Sink or swim. So, my English is New York City street English.”
Pasakarnis has viewed every obstacle as a learning moment since she first began her career, and her decades of work in 3D design is built on that sentiment. During a candid conversation, Pasakarnis shared how she got to where she is today, her aspirations for 3D design at Kontoor and her thoughts on why 3D design is the right fit for the industry.
Why has Kontoor and its brands turned to 3D design?
In large companies like ours, many different people and functions will help deliver a product from concept to development to the consumer. To ensure we’re all working toward the same end result, we have to show what you think to other people, other departments. You need to communicate. This is where the 3D technologies are amazing. They are very realistic, very visual, and they work exactly as in real life.
How does denim, in particular, benefit from 3D design?
Denim is a very complex product. Why? Because it’s washed. It has completely different properties before and after wash. The fabric is going to shrink. So we have to account for those differences in the design process so that it shrinks to exactly the measurement we're expecting.
And that’s the beauty of the product—it’s inconsistent. But the virtual world is perfect. We can use after-wash fabrics in our designs that tell us exactly how the garment will fit. We even have a virtual pressure map that can tell us how our products will feel on the body. The end result is a garment that fits true to size and exactly as we intended going into the design.
Where do you see the future of 3D design heading?
Right now, we’re working across teams to leverage virtual prototypes: from design to virtual live reviews, virtual catalogs, customization and manufacturing. It’s going to lead to a lot of usage of our virtual assets and that’s when we’re hoping to see significant savings in the prototyping process.
More About Margarita:
- Number of languages spoken: Three—though she’s learned and lost others along the way.
- Favorite item of clothing from Kontoor Brands: This Wrangler t-shirt and the three dozen Wrangler jeans in her closet.
- Hobbies when off the clock: Playing classical music on the piano. After hiking, she calls wearing high heels her “second favorite exercise.”
- Favorite part of working at Kontoor: “I love the products, the consumer and the people I work with.”